Две недели назад в Барнауле начался дорожно-строительный сезон, и специализированные организации приступили к обновлению покрытия на улицах. Для обеспечения работы все крупные подрядчики содержат собственные асфальтобетонные заводы, на которых производят смесь. Корреспонденты «Вечёрки» побывали на заводе при «Автодорстрое», где увидели полный производственный цикл и узнали, почему технологию приготовления асфальта сравнивают с кулинарным мастерством.
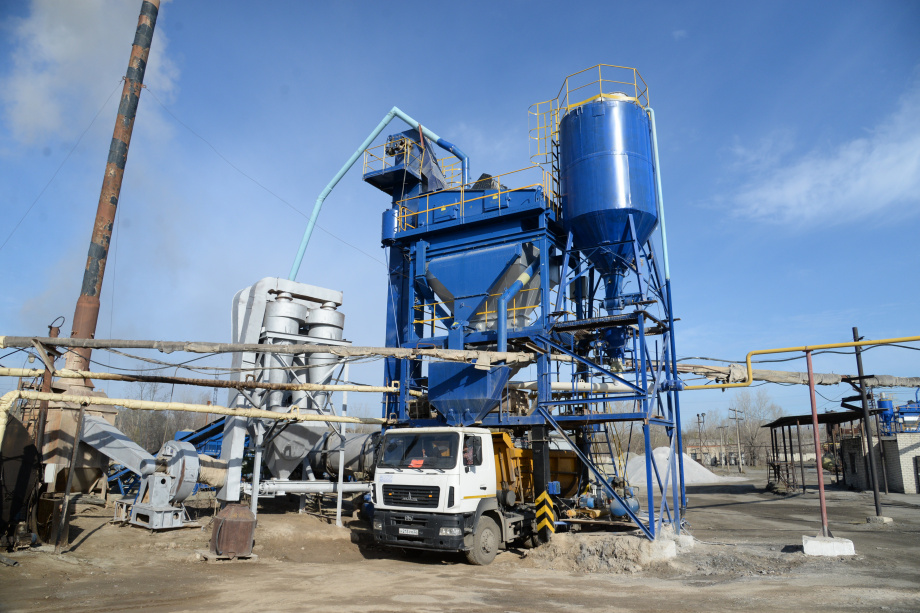
Было и стало
В начале 2000-х этот завод можно было определить издалека, даже не зная точно, где он находится — производство асфальтобетона выдавал плотный иссиня-чёрный дым, который образовывался при варке смеси. С тех пор как предприятие перевели на природный газ, оно стало гораздо более экологичным: теперь по едва уловимой белой дымке и не скажешь, что здесь находится «грязное» производство — именно так долгое время называли предприятия по выпуску асфальта.
В 9 часов утра на производственной площадке в промзоне Центрального района вовсю кипит работа, и на погрузке только что произведённого горячего асфальта уже стоит 6-кубовый КамАЗ. Его водителя, Алексея, инструктируют: все сегодняшние партии готовятся для латочного ремонта нескольких участков улиц Северо-Западной и Юрина.
— Нам заказали 150 тонн смеси. Этот объём мы можем выдать к обеду: мощность наших установок позволяет настолько интенсивно работать. Но будем корректировать темпы производства, чтобы наши коллеги в течение всей рабочей смены бесперебойно получали горячий асфальт, — рассказывает Сергей Ломакин, начальник асфальтобетонного завода.
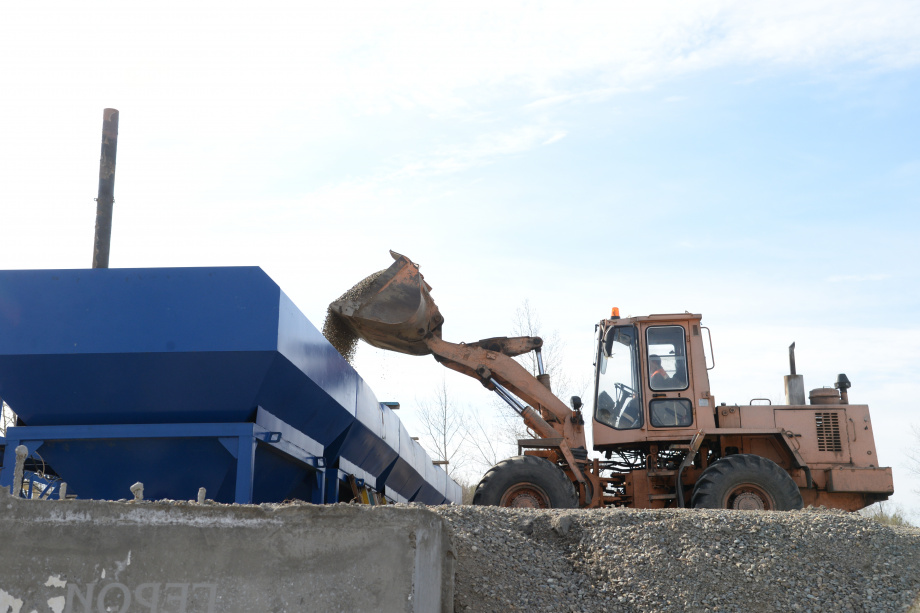
АБЗ несколько отличается от промышленных предприятий в привычном нам понимании: вместо помещений — открытая площадка, на которой смонтированы производственные агрегаты и установлены бункеры для хранения битума и минерального порошка, песок и щебень лежат под открытым небом. Так выглядел завод в 1994 году, когда его построили, таким является и сейчас — соответственно требованиям производственной логистики. За 27 лет изменилось только оборудование, на котором непосредственно готовится асфальт.
На предприятии несколько лет назад повысили долю собственного производства в целях снижения себестоимости асфальта и начали выпускать минеральный порошок, который раньше закупали за пределами Алтайского края за баснословные деньги.
Варщик асфальтобетонной смеси Дмитрий Новиков работает на предприятии уже 22 года. Он вспоминает, что в 1990-х годах кабина оператора, откуда ведётся управление производственным процессом, напоминала кабину самолёта: на панели огромное количество кнопок, рычагов, стрелок, ключей. Все их запомнить было сложно, особенно новичку, поэтому подписывали.
— Смесительные установки были полуавтоматическими, и это требовало от нас ежеминутной сосредоточенности и внимания. При подаче каждого компонента — щебня, битума, песка, минерального порошка — нужно было следить за показателями на весах и вовремя переключать рычаги. Недовес одного материала или перевес другого приводил к браку всей партии. Плюс контролировали ещё десяток самых разных параметров, так что к концу смены голова кругом шла, — продолжает Дмитрий Анатольевич и признается, что сейчас работать на полностью автоматизированном оборудовании — просто рай. На компьютерном мониторе отображаются все производственные параметры, а потому присутствие оператора необходимо лишь для контроля: установить количество замесов, следить за температурой и мониторить исправность пневмосистемы.
Пять компонентов
С этого года дорожники «Автодорстроя» перешли на использование пятифракционного асфальта вместо 4-компонентного — это требование времени, позволяющее повысить долговечность покрытия. Потребовалась модернизация оборудования, но технологическая цепочка при этом не изменилась. Асфальт производится путём смешивания в определённых пропорциях щебня, песка, битума и минерального порошка.
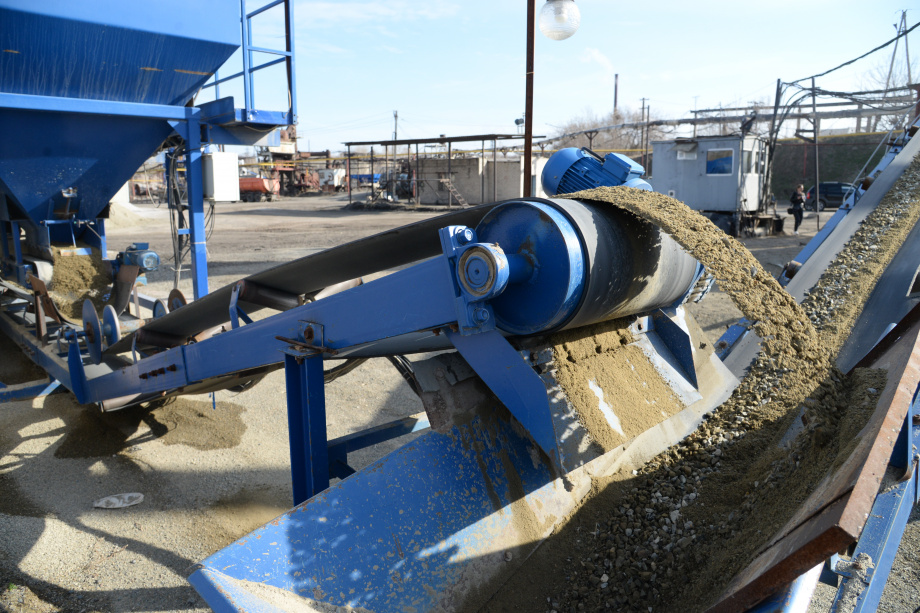
— В процессе варки асфальта важно выдержать пропорции, поэтому мы часто сравниваем этот процесс с изготовлением теста. Ведь получится некондиция, если положить недостаточно дрожжей, слишком много муки или использовать горячую воду. У нас также, — объясняет Сергей Ломакин.
Речь его перебивает грохот — началась сортировка щебня. А его тут пять видов, и каждый должен быть в строго определенном количестве. Затем по конвейеру поднимается песок, который после обработки, автоматического взвешивания и сортировки попадет в смеситель к минеральной части будущего асфальта. Главная сложность в производстве асфальта — подать в смеситель щебень и песок, потому что компоненты должны быть сухими и нагретыми до температуры 130–140 градусов. Этого добиваются, пропуская их через сушильный барабан, который работает от сжигания газовоздушной смеси.
После добавления минерального порошка и кипящего битума в смеситель с минеральным сырьем начинается финальный процесс — тщательное и многоступенчатое перемешивание всех компонентов. Спустя некоторое время из горловины смесителя в кузов КамАЗа поступает густая чёрная масса температурой 130–140 градусов, не больше и не меньше. Если асфальтобетон перегреть, битум потеряет свои вяжущие свойства и асфальт превратится в сухую крошку. В обратном случае — компоненты плохо перемешаются, и такой асфальт будет недолговечным.
Отъехав к специальной площадке, камазист поднимается на лестницу и закрывает кузов машины тентом, который не даст асфальтовой смеси остыть, пока его довезут до места назначения.