В Барнауле действует единственное на Алтае производство крепежных изделий, предназначенных для строительно-отделочных работ. В этом году предприятие с помощью господдержки расширило производство с тем, чтобы потеснить на российских стройках импорт.
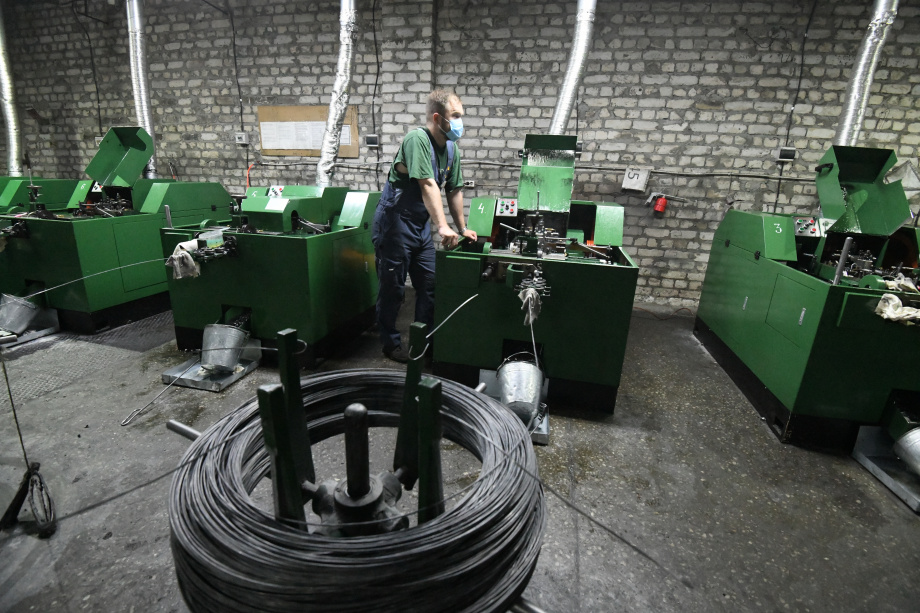
Фото: Андрей Чурилов
Первый этап
В цехе ООО «Рамас» 14 станков для производства саморезов, а управляют ими всего четыре человека в смену. Автоматизированная линия протягивает проволоку из огромных бобин, нарезает болванки нужного размера, формирует шляпку и резьбу, после чего изделие цементируется в печи.
- Термообработка необходима для повышения прочности самореза, что позволяет его вкручивать в дерево или тонкий металл, – объясняет руководитель предприятия Максим Драный. – При нагреве до 900 градусов происходит формирование сложной поверхности, после чего заготовка падает в закалочную ванну для закрепления верхнего слоя.
У печи, в отличие от других станков, всегда стоит один человек. За раз она вмещает не более 40 кг саморезов, при максимальной загрузке двух печей изготавливается до 40 тонн изделий в месяц. На производительности печей, собственно, и завязан весь производственный цикл. В пути – новая печь, которую предприниматель заказал в рамках модернизации производства. Она позволит закаливать до 120 тонн изделий в месяц без увеличения штата. Печь полностью автоматизированная – сама по всему циклу продвигает изделие, нужен сотрудник лишь на входе и выходе для технического контроля. Для достижения производительности, как у новых закалочных печей, при имеющемся оборудовании необходимо было бы увеличить штат в 5-6 раз.
- Сегодня самая затратная часть себестоимости изделия – это оплата труда, – уточняет бизнесмен. – Благодаря новому оборудованию количество людей на единицу изделия будет меньше, что позволит снизить себестоимость.
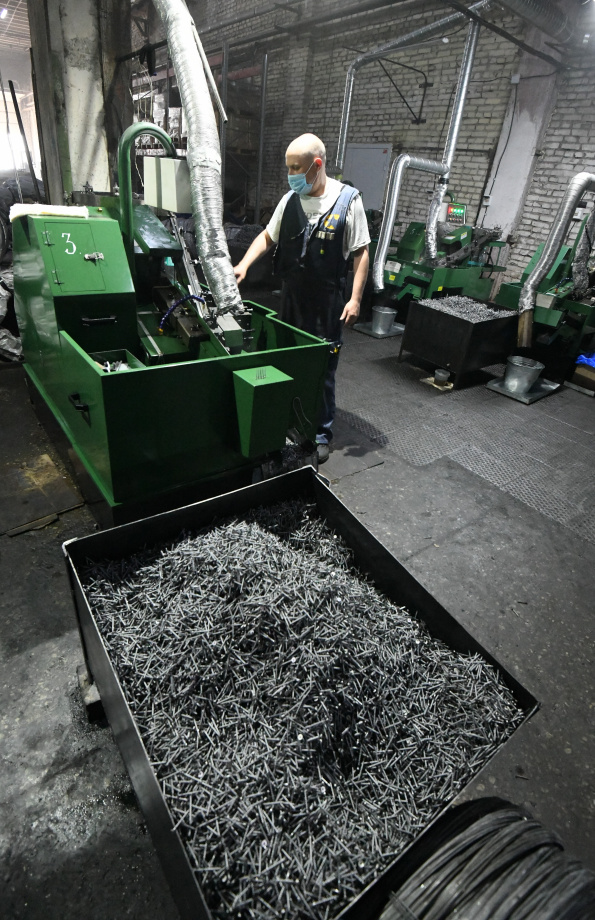
Заработная плата специалистов в данной области на уровне средней по региону, но и возможности для роста есть. Персонал приходится обучать здесь же, на производстве. Наладчик становится опытным лишь спустя год после начала работы. При желании и упорстве, любой оператор может вырасти в наладчика, а это уже квалифицированный специалист, и оплата труда другая.
- Новая печь – это первый этап модернизации производства, – рассказывает Максим Евгеньевич. – Второй этап – это увеличение количества станков, 14 единиц тоже в пути. Третий – приобретение нового оборудования. К примеру, калибровочный станок даст возможность снять зависимость от поставщиков сырья. Проволока поставляется не всегда нужного качества, станок позволяет делать необходимую для входа проволоку – без скачков в диаметре, оснастка не ломается.
120 тонн саморезов в месяц сможет производить предприятие после полного обновления оборудования.
Построено на энтузиазме
А начинал Максим Драный практически с гаражной мастерской, где на трех станках отливали пластиковые дюбели под собственной торговой маркой. Но масштабы производства не удовлетворяли амбициозных планов предпринимателя, и вскоре он решил изготавливать под них гвозди-шурупы, но после детального изучения вопроса остановился на саморезах.
Новое производство предприниматель открыл в 2018 году, и уже через два года решился на расширение. На обновление оборудования требовалось 40 млн. руб. Во избежание больших единовременных затрат он обратился за кредитом в банк, но собственного обеспечения не хватило. Центр предоставления гарантий Алтайского фонда развития малого и среднего предпринимательства помог с поручительством на 14 миллионов.
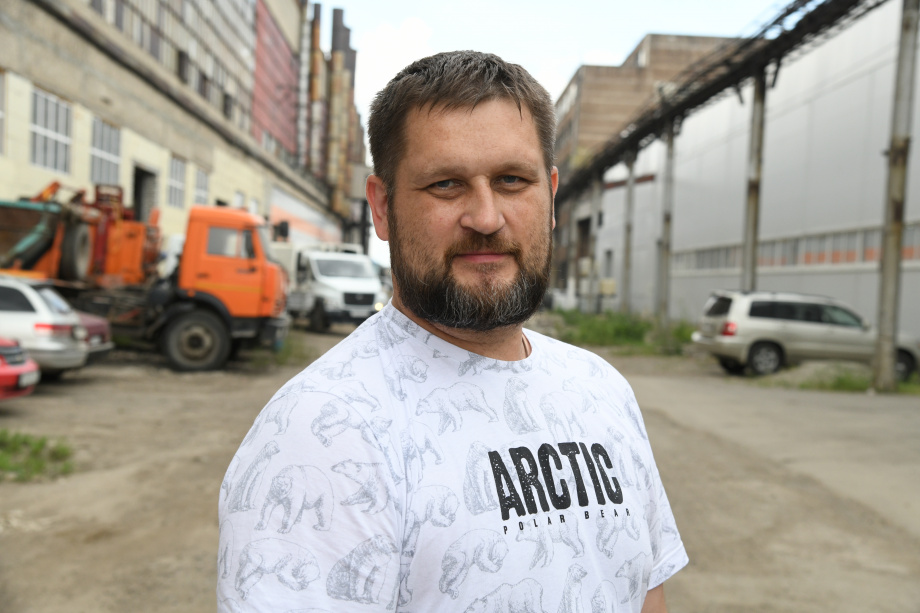
Фото: Андрей Чурилов
Предприниматель решился на расширение производства, поставив перед собой амбициозную задачу – потеснить конкурентов с Азии. Крепежный сегмент на российском рынке на 90% представлен Китаем. В России не больше пяти подобных производств, не считая гигантов, вроде Новолипецкого меткомбината – Метиз. Дело в том, что советская промышленность специализировалась преимущественно на машиностроительном крепеже, ничего кроме гаек, болтов и гвоздей в арсенале строителей и не было. А иностранные производители вышли на рынок с крепежами для строительно-отделочных работ. Помимо ассортимента, зарубежные поставщики завоевывают рынок ценовым демпингом. Как утверждает бизнесмен, Китай, к примеру, занижает стоимость метизов при ввозе, уменьшая вес изделия. К примеру, российский саморез 3,5х41 мм весит 1,95 г, а китайский – 1,81. Соответственно, при ввозе поставщик экономит на пошлине, за счет чего снижает конечную цену. Изменения не критичны, но головы таким саморезам срывают при закручивании. А что требования? Данные крепежи не относятся к несущим сложные конструкции, поэтому на них нет строгих требований, как, например, на болты с дюбелями для крепления фасадов. И как конкурировать в таких условиях, не снижая качество изделий?
- Мы планируем снизить себестоимость продукции за счет модернизации оборудования, что позволит увеличить объемы производства, – говорит Максим Евгеньевич. – Маржинальность нашего вида производства невысокая, эффективности можно добиться только за счет увеличения объемов, и за счет автоматизации. Когда мы открывали дело, на первом плане были энтузиазм и уверенность в том, что такое производство в России должно быть.
Сбыт определяет
Сегодня компания изготавливает два вида продукции, планирует гвозди-шурупы. Для их производства необходимо то же самое оборудование, кроме печи. Тем более с рынка ушел крупный производитель. Также собирается изменить размерную линейку.
Главная проблема каждого производства – это сбыт. Компания взаимодействует с федеральными торговыми сетями.
- При реализации в сети маржинальность продукции выше, нежели оптовикам, но и сложностей тоже больше, – отмечает предприниматель. – Во-первых, в сети сложно попасть. Нужно быть уверенным, что сможешь обеспечить требуемый объем поставок. С увеличением производства может возникнуть другая сложность – весь объем продукции фасовать невозможно, а в сети необходима фасовка. С приходом нового оборудования нарастим объемы, часть продукции будем поставлять в сети, часть оптовикам. Есть планы по выходу на экспорт, пока в ближнее зарубежье – Казахстан, Украину.