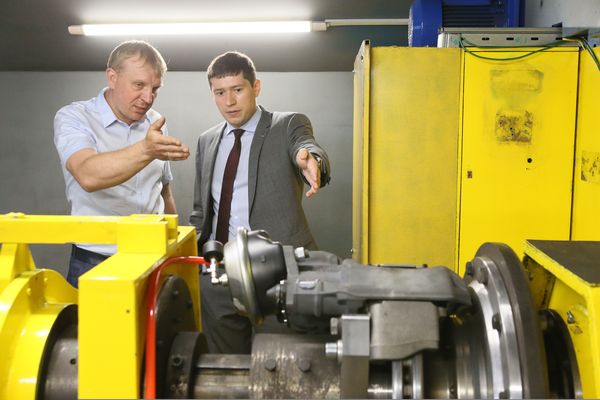
Артём Шамков: «Качество продукции нашего завода на соответствие требованиям ЕС подтверждено испытаниями в Испании».
Фото Владимира Вдовина
Фото Владимира Вдовина
Барнаульский завод АТИ является поставщиком ведущих корпораций страны: «Росатома», «Роснефти», «Газпромнефти», РУСАЛа. Гиганты грузового автомобилестроения – МАЗ, БелАЗ, УралАЗ, МоАЗ, ТАиМ, МТЗ – используют в своих автомобилях тормозные колодки АТИ.
В начале года группа инженеров побывала в командировке в Испании, где были проведены сертификационные дорожные испытания дисковых тормозных колодок для грузовых автомобилей иностранного производства на соответствие требованиям ЕС.
Такие типы колодок применяются в тормозных узлах грузовых автомобилей Mercedes-Benz, MAN, DAF, Scania и Iveco. По заключению специалистов, тормозные колодки безасбестовой композиции полностью соответствуют требованиям Европейского Союза.
- За этим успехом стоит кропотливая работа наших специалистов, – отметил генеральный директор Барнаульского завода АТИ Артём Шамков. – Состав и рецептура безасбестовой композиции – это ноу-хау предприятия и является закрытой информацией. Компоненты уникального состава подбиралась в течение года по граммам, по десятой, сотой доли процента. Композиция получилась стабильная, качественная, с хорошими тормозными характеристиками, высокой ходимостью и бережным отношением к тормозному диску.
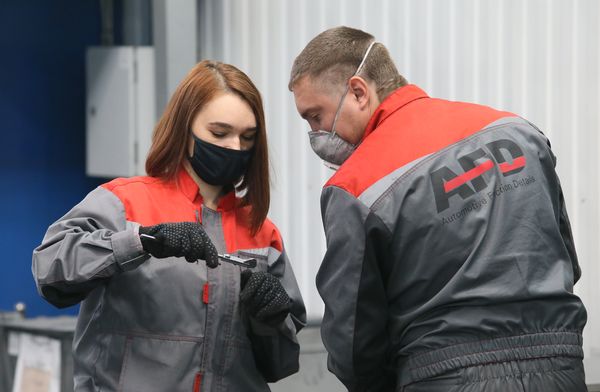
Фото Владимира Вдовина
Приобретено современное испытательное и лабораторное оборудование. Дополнительно к стенду с нагрузкой на ось до 3,5 тонн, который на протяжении последних лет использовался на предприятии, в 2019 году установлен динамометрический стенд английского производства, способный давать нагрузку на ось до 30 тонн. Технические характеристики нового стенда позволяют проводить на нем натурные испытания тормозных колодок не только для автомобилей, но и для железнодорожного транспорта в условиях, максимально приближенных к реальным.
Для Алтайского края это важное событие, поскольку такого оборудования за Уралом нет, и в России подобных испытательных центров всего два. Сейчас идет процесс сертификации динамометрического стенда, что позволит проводить испытания для сторонних компаний.
- Для нас даже сейчас, в эпоху цифровизации самое ценное – это коллектив, который может мобилизоваться и управлять процессом в самые сложные времена. Это важный элемент успеха, – подчеркнул Артём Шамков. – Когда на ключевых постах грамотные и эффективные специалисты, можно внедрить и освоить новую технологию, без проблем запустить или отремонтировать оборудование. А без специалистов – это невозможно.