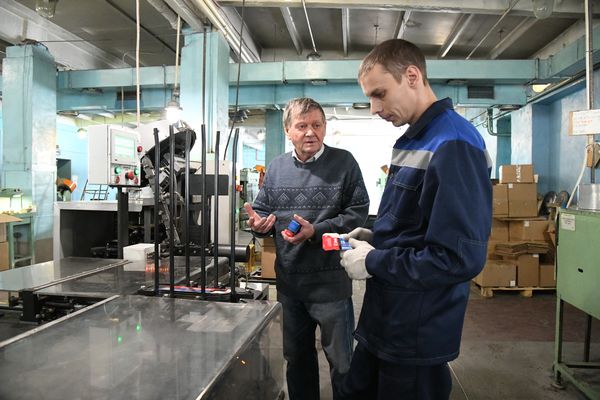
Анатолий Климов рассказывает молодому сотруднику, как нужно работать на новом станке.
Фото Андрея Чурилова
Фото Андрея Чурилова
Стаж, вместивший в себя целую жизнь, – 63 года. Именно столько день за днем проработал на станкостроительном заводе Анатолий Климов, которого здесь называют легендой. Он прошел путь от ученика токаря до главного специалиста конструкторского бюро. Профессионал, великий труженик, наконец просто добрый и отзывчивый человек.
В токари пойду!
Он родился перед самой войной, а потому принадлежит поколению, которому выпало развивать страну после ее восстановления. Сегодня практически в любом цехе завода есть хоть один станок, сделанный Анатолием Климовым или под его непосредственным руководством. А ведь много лет назад он пришел на проходную устраиваться учеником токаря, именно об этой профессии мечтал с детства.
- Я вырос на Дальнем Востоке. В городе Сковородине было большое железнодорожное депо, на котором работал сосед, несколько раз водивший меня на экскурсию, – вспоминает Анатолий Петрович. – Видел, как рабочие трудятся. Отец погиб на фронте, и мы вместе с мамой переехали к родным в Барнаул, здесь я получил школьный аттестат и пошел устраиваться учеником токаря. Время было трудное, послевоенное, многие предприятия снимали военную продукцию, переходили на рельсы мирной жизни, и рабочие были не нужны. Я обошел ряд заводов и везде получил отказ.
И все же Анатолию Климову удалось устроиться на станкостроительный, из ученика он быстро вырос до токаря.
- Завод тогда был другим, не таким зеленым, ухоженным, ведь в те времена все силы бросали на развитие производства, не было и многих цехов, – вспоминает он. – И все же для меня он стал вторым домом, который ни при каких обстоятельствах – а их, начиная с развала Советского Союза, возникало немало – бросить не хотелось.
После армии, продолжая работать токарем, получил высшее инженерное образование в политехническом институте, а уже через несколько лет стал начальником производства, в подчинении которого были 2000 человек и семь цехов.
- 1 мая по традиции мы всем коллективом шли на демонстрацию, – говорит Анатолий Петрович. – Колонны рабочих всегда выглядели внушительно, с транспарантами, флагами, с улыбками на лицах! Люди понимали, что они опора экономики не только нашего города, но и всей страны, ведь продукция станкостроительного расходилась далеко за пределы края, она и по сей день пользуется спросом в стране и за рубежом.
Выйдя на пенсию, он перешел в конструкторское бюро и уже больше 10 лет создает новые станки, которые не только облегчают работу, но и увеличивают объемы производства.
84 146 человек в Барнауле заняты на производстве.
В ногу со временем
Застать Анатолия Климова в кабинете сложно, он в лаборатории среди станков, чертежей и обязательно с новой идеей. Мы его встретили в одном из цехов. Именно здесь идет изготовление и упаковка патронов. Большой цех, по периметру стоят огромные коробки с готовой продукцией, шум от работающих станков заставляет подходить ближе к собеседнику, чтобы услышать его слова. Да здесь никто и не болтает, люди приходят сюда работать.
- Еще десять лет назад этот цех выглядел совершенно по-другому, – рассказывает Евгений Попов, заместитель начальника по технической части цеха № 21. – За столами сидели женщины, которые вручную собирали упаковки и раскладывали по ним патроны. Когда заказ был срочным и объемным, на помощь приходили люди из заводоуправления. Сегодня многие операции выполняет станок, сделанный Анатолием Петровичем. Рабочий лишь следит за процессом, вовремя закладывая в «магазин» контейнеры для упаковки. Все остальные операции делает станок, контролируя при этом качество продукции.
Анатолий Климов с улыбкой признается: всегда читал много технической литературы, сейчас на помощь пришел Интернет – безграничный информационный ресурс.
- Мы не можем использовать готовые упаковочные станки по простой причине: у нас уникальная продукция, – отмечает Климов. – Оборудование можно сделать по заказу, но оно будет в разы дороже и его настройка потребует много времени. Поэтому приходится творить. Создание нового станка всегда начинается с постановки цели, вот этот рождался недолгий период, а этот – около года.
Творческая разработка входит в оргтехплан, и она должна быть доведена до конца в четко обозначенные сроки. Обязательно формулируется, почему не устраивает старое оборудование. Это может быть низкая производительность, сложность в обслуживании, большая стоимость ремонта. К примеру, завод не может самостоятельно изготовить электронные датчики, электрические, пневматические устройства. Порой рентабельнее приобрести многие готовые комплектующие, если позволяют финансовые возможности. Задача инженера заключается в том, чтобы максимально автоматизировать ручной труд на упаковке, а лучше – исключить его полностью.
Всегда рады молодежи
Анатолий Климов с улыбкой замечает, что супруга давно просит заканчивать с работой и больше заниматься внуками – их трое. Но не представляет он себя без проходной станкостроительного, без этой профессии, которая подходит для рук и ума, для души и сердца. И он рад, что молодежь потянулась на завод.
- Помните в «Белых росах»: на завод пришел, а поговорить не с кем? – говорит он. – Вот и я уже не всех знаю. Приходит молодежь, а это значит, есть кому оставить свое наследство.
Сейчас на станкостроительном трудится более 2500 человек, почти 40% из них – моложе 35 лет.
- Развивая производство, на заводе никогда не забывали о его рабочих, не зря именно они, люди, считаются основой предприятия, – комментирует Евгений Попов. – Мы имеем свой санаторий-профилакторий, детский оздоровительный лагерь, лыжную базу. Особое внимание – ветеранам, для них организуем и праздники, и общение. Не забываем и о молодежи, мы вернулись к системе наставничества, традиционными стали конкурсы профмастерства, проведение спортивных состязаний. Поддерживаем и тех, кто приобретает жилье в ипотеку, помогая оформить кредит. Я думаю, что пора уже школьникам повернуться лицом к рабочим профессиям и стремиться получить специальность, которая будет не просто кормить всю семью, но и даст уверенность в будущем.
Виктор Яшкин, гендиректор холдинговой компании «Барнаульский станкостроительный завод»: «В свое время при производстве теплообменников мы столкнулись с отсутствием пресса определенной мощности для формования пластин, купить его было баснословно дорого для завода. Группа СКО под руководством Анатолия Петровича спроектировала и собрала этот пресс, который и сейчас работает».