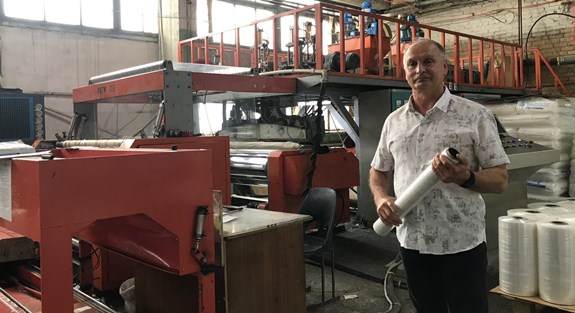
Вячеслав Липин открыл направление изготовления стретч-пленки, ориентируясь на потребности региональных заказчиков.
Фото Алисы Тростниковой
Фото Алисы Тростниковой
Старт вслепую
Вячеслав Липин принадлежит к поколению предпринимателей, становление которых пришлось на становление рыночной экономики. Перепробовал разные виды коммерции, пока однажды в середине 1990-х партнер не предложил ему заняться поставками колбасной оболочки для мясоперерабатывающих цехов. Направление оказалось перспективным, молодая компания на несколько лет крепко обосновалась в новой нише. По запросам клиентов приобрели полиграфическое оборудование, чтобы наносить печать на колбасную оболочку. Рынок полиэтиленовой упаковки в России только зарождался, до 1998 года львиную долю составлял импорт. С одной стороны, найти нишу было достаточно просто. С другой, не имея опыта в производстве, приходилось зачастую действовать вслепую.
- Колбасная оболочка шириной 8 сантиметров, а печатную машинку по незнанию приобрели метровую, – смеется теперь Вячеслав Липин. – Не сосчитать, сколько колбасной оболочки испортили. Тонкости производства постигали непосредственно в процессе – не у кого было спросить совета. Потом не очень успешно пытались наладить печать на упаковках под молоко. Зато появился опыт, и мы решили продолжать работать в сегменте упаковки. Приобрели экструдер, начали сами изготавливать фасовку для пищевки – для пельменей, лаваша. Мы первыми в регионе придумали печатать упаковку для семечек.
Потребности рынка буквально в геометрической прогрессии увеличивались в сторону качества продукта. Нужно было модернизировать производство, чтобы успевать за запросами заказчика. Сами изготавливали пленку, сами печатали этикетки на современном полиграфическом оборудовании. Сначала применяли одно-двухцветную печать, потом трех-четырех. 6-8-12-цветная полиграфия требовала более серьезных технологий, чтобы конкурировать с крупными столичными производителями. Мы с нашим скромным бюджетом обосновались в сегменте недорогостоящей упаковки и постепенно перешли на производство фасовочных пакетов.
60 тонн пленки ежемесячно выпускает ООО «Промупаковка».
Грант на стретч
Спустя год после определения нового курса заключили контракт с крупным сибирским ритейлом на поставку полиэтиленовых пакетов и мешков. Партнерские отношения длились почти 10 лет. В 2015 году алтайскому предприятию предложили войти в группу компаний холдинга. По словам Вячеслава Липина, перспективы сулили заманчивые, но продавать свое детище барнаульские предприниматели отказались. И как показала жизнь, решение было верным – нынешней весной ритейл обанкротился. За год до этого торговая сеть начала собственное производство упаковки. Но поступила по-партнерски: не враз оборвала договоренности, а в течение двух лет, что позволило постепенно найти новые каналы сбыта.
Сегодня барнаульское предприятие работает со всеми торговыми сетями Сибири, упаковывает продукцию алтайских пищевиков. Компания не стоит на месте, параллельно развивает современные направления, одним из таковых является стретч-пленка. Спрос на данный вид упаковки растет с каждым годом, и ввиду низкой насыщенности рынка этот сегмент становится привлекательным для инвестиций.
- Хотя новое направление открывалось на базе работающего предприятия, требовалось специальное оборудование, – рассказывает Вячеслав Геннадьевич. – Схожие технологии, состав из одинаковых полимеров, но способ получения пленки отличается методами экструзии. Открытие линии требовало финансовых вложений. Поскольку долго и эффективно работаем с администрацией Барнаула, знаем все формы поддержки предпринимательства, то заявили свой проект на грант. Успешно его защитили. С учетом софинансирования поддержка покрыла 30% стоимости линии.
Прибыль в две копейки
По словам Вячеслава Липина, упаковка – достаточно широкий и объемный рынок, но не такой доходный продукт, как кажется. Многие думают: пленка везде нужна, сейчас купим станок, наделаем пакетов и быстро отобьем вложения. Но процентов 90 новоиспеченных предпринимателей, столкнувшись с производством, либо меняют направление, либо уходят с рынка.
- На самом деле с каждого изделия прибыли 1-2 копейки, – приводит цифры бизнесмен. – Сырьевая составляющая в продукте значительная – до 80 процентов. Поэтому важно строго следить за технологией, контролировать расход материалов на каждой операции. Предприятие занимается вторичной переработкой только собственных отходов. Без этого производством упаковки нет смысла заниматься, ведь даже при отлаженных технологических процессах брак составляет от 1 до 15 процентов.
Предприниматель намерен и дальше расширять производство пластиковой упаковки, несмотря на предостережения экозащитников в возможном отказе от пластиковой фасовки.
- За пластиком будущее, – уверен Вячеслав Липин. – Даже изделия из металла заменяются пластиком, из него делают человеческие органы. Тот же лес сложнее вырастить, чем изготовить пластик. Вопрос в рациональном его использовании. Правильно организованный сбор и переработка пластика экономит природные ресурсы, снижает себестоимость и цену и не вредит окружающей среде. К сожалению, наше государство немного запоздало в решении данного вопроса. Хотя есть прекрасные мировые примеры. В Германии перерабатывается до 90 процентов пластика, в Японии мусороперерабатывающий завод стоит в центре города и никому не мешает.
Еще один вариант снижения вредного влияния пластика на окружающую среду – внедрение в производство добавок, ускоряющих процесс разложения. Мы одними из первых начали использовать их в своем производстве. На начальном этапе экспериментировали с добавками, хранили пакеты при определенных условиях, чтобы выяснить, сколько времени необходимо на их разложение. Там, где больше биоразлагающих добавок, через три-четыре месяца пакет превратился в труху.
Вячеслав Липин: «Бизнес на упаковке выгоден, когда правильно построено предприятие, отшлифована экономика и слаженно работает команда. Есть много других, более прибыльных отраслей. Здесь просто нужно пахать».